Ballistic
helmets
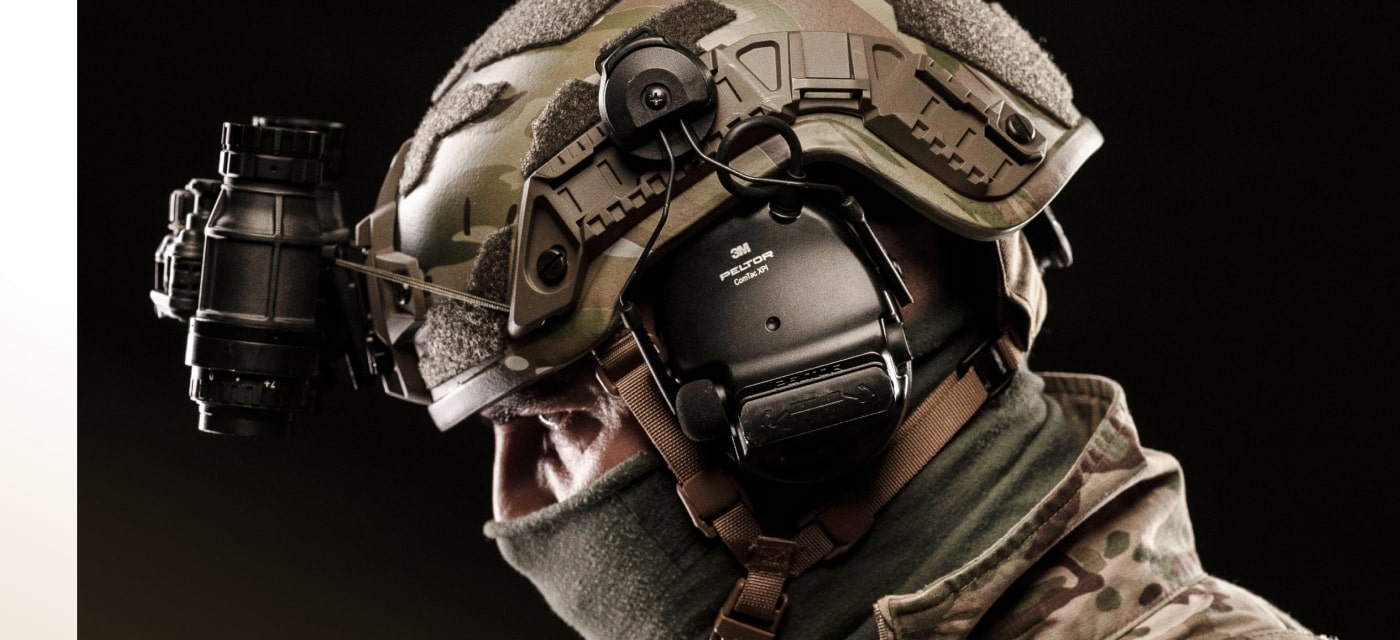
We use Kevlar® aramid for our helmets
Kevlar® is a specific kind of aramid fiber especially known for extreme strength and heat resistance making it well suited for ballistic equipment.
Impact testing shows that helmets made with Kevlar® fiber have a superior structural integrity to help enhance survivability in ballistic impacts.
how our ballistic helmets are made
-
01Turn unprocessed Kevlar fibers into ballistic fabricFirst step is to turn the unprocessed Kevlar fibers into a ballistic fabric sheet. That is accomplished by following a specific weaving technique or pattern where the Kevlar threads form a dense structure.
-
02The fabric is cut into the specific shapesNext up, the fabric is cut into the specific shapes for the helmets and layered to form the structure of the helmet. The layers must lie in a specific order and rotation and the precise number of layers varies depending on the desired protection level for the different kinds of helmets.
-
03Pressed in a moldThe layered fabric sheets are now placed into a helmet mold. In the mold constant heat and pressure are applied for a fixed amount of time using a hydraulic press to shape the material into the helmet form, creating a solid and rigid structure.
-
04Trimming processAt last all excess material is carefully trimmed off. This ensures the helmet achieves the intended shape and dimensions. After trimming, the edges are smoothed to remove sharpness and prevent discomfort during wear.
-
05The helmets are paintedThe helmets are sandblasted and smoothed to achieve the final shape. The helmets are placed in a painting line getting sprayed either black, OD green, multicam, multicam black or coyote brown which are the colours our helmets are available in.
-
06The helmets are equipped with additional componentsComponents such as rails, memory foam padding, the BOA Fit buckle system, shroud and other fittings are added before being packaged and prepared for distribution.
-
07Quality checkEven the smallest imperfections in materials or the manufacturing process can compromise the quality and thereby the integrity of the helmet. That is why it is utmost important that every stage of production has its own unique set of checks. And every single helmet is going through a final quality inspection by our team before leaving our facility in Denmark.
Our helmet colours
The colour you choose for your helmet is important because it can affect visibility and concealment in different environments all over the world.
Black, OD green, multicam, multicam black or coyote brown
If needed you can also buy a textile helmet cover to make sure that the helmet blends with the surroundings, enhancing your ability to remain undetected and safe in tactical situations.
Our ballistic helmets offer greater protection than the NIJ standard 0106.01
Our bulletproof helmets are made to meet every need.
They offer greater protection than the standard NIJ standard 0106.01, as they are tested against .44 Magnum, .357 SIG and 9 mm FMJ, with an extremely low back face deformation.
Furthermore they offer a fragmentation protection of 660 m/s according to STANAG 2920.
The fact that our helmets maintain exceptional structural integrity means they do not delaminate when subjected to a bullet or fragmentation. This also contributes to their durability, ensuring they perform well in various compression tests. As a result, the helmets have a long lifespan, which is why we confidently offer a 10-year warranty.
Read our article on NIJ standard 0106.01 for ballistic helmets for much more information.
-
WWIDuring World War I, soldiers were first equipped with simple steel helmets, such as the British Brodie helmet. It was designed to protect the soldiers from shrapnel, debris, and other battlefield fragmentation hazards. The British Brodie helmet offered better protection than cloth caps but it had limitations against direct bullet strikes. The steel construction made the helmets heavy but these early helmets marked a significant advancement in battlefield protection, laying the groundwork for future developments in helmet technology.
-
WWIIDuring World War II, weight, comfort, and protection level influenced the redesign of the fragmentation helmet to become the famous M1 helmet. The helmet had an outer metal shell and a molded inner shell to attach the adjustable suspension made of cotton webbing and leather. The outer shell could be separated from the liner and used as a bucket, bowl or even a cooking pot. In late 1942 the helmet cover with camouflage patterns was introduced.
-
1960sIn the early 1960s, the U.S. Army set their goal on replacing this two-part helmet design with a single-walled, lighter and more protective helmet. With the invention of Kevlar in 1965, it became obvious that this high strength polymer could be of use. In 1972 Kevlar was commercially available and Kevlar helmets, such as the PASGT from 1983, suddenly provided ballistic protection while being lighter and much more comfortable than steel.
-
Modern timesOver the years, materials like Twaron, Dyneema, and Spectra have led to further enhancing protection, durability, and weight reduction. Modern ballistic helmets like our own PGD-ARCH GEN3 ballistic helmet, are now highly advanced, offering modular features, improved ergonomics, and compatibility with communication systems and other gear.